The key to the Vietnam textile industry’s dual transformation
Digitalization and greening are the twin transformation imperatives for the textile and garment industry as it moves toward higher value, green growth, and sustainable development—meeting increasingly stringent demands from global markets.
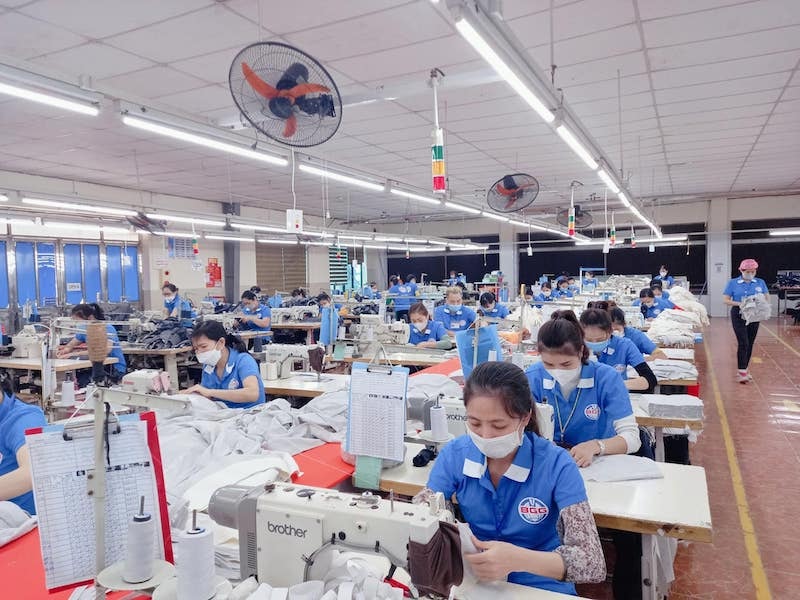
In 2025, the textile industry targets USD 48 billion in export turnover.
In 2025, the textile industry aims to reach an export turnover of USD 48 billion. Achieving this ambitious goal will require significant effort, especially as key markets are now codifying standards on emissions, traceability, and environmental certifications. These new regulations are forcing enterprises to “go green” or risk being excluded from global supply chains.
At the same time, companies must also compete in terms of productivity, cost, and flexibility, as brands increasingly prioritize small-batch orders with fast delivery times.
According to Mr. Trương Văn Cẩm, Vice President and General Secretary of the Vietnam Textile and Apparel Association (VITAS), the biggest current challenge is increasing value-added. Vietnam's textile industry still largely relies on outsourcing; despite high export value, the actual retained value remains relatively low. To break through, companies must invest in technology, design, material autonomy, and digital transformation.
In addition, amid a global push for net-zero emissions and responsible consumption, "greening" the textile industry is no longer optional, but a survival condition for future growth.
“Without timely transformation, the textile industry may lose access to high-end markets. Greening is a matter of survival, no longer just a trend,” emphasized Mr. Trương Văn Cẩm.
Thus, digitalization and greening are no longer superficial choices—they are a strategic duo for Vietnamese textile firms to enhance competitiveness, improve business efficiency, and create new value.
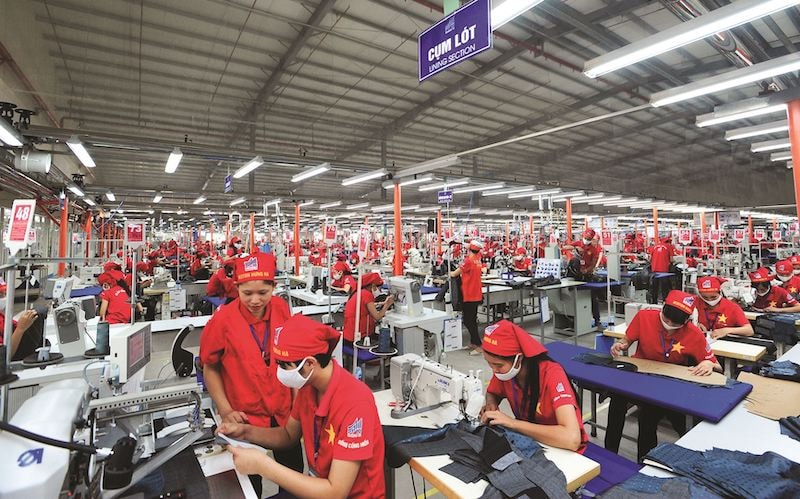
Key markets are enforcing regulations on emissions, traceability, and environmental certifications—forcing businesses to green operations or risk exclusion from global supply chains.
Recognizing this need, many pioneering enterprises have proactively invested early in clean technology, energy-saving processes, and modern wastewater treatment systems instead of waiting for regulations to become mandatory. This is not only preparation for the future but also a strategy for gaining a competitive edge now.
For example, Garment Corporation 10 (May 10) has replaced 90% of coal-fired boilers in its factories with biomass pellet boilers, aiming to reduce carbon emissions by 20,000 tons in 2025. The company also plans to fully install rooftop solar panels at its facilities. Additionally, recycled fibers currently make up 30–50% of May 10’s apparel products. The corporation partners with fiber producers to recycle surplus materials into new fibers for production.
Similarly, Bac Giang Garment Corporation now generates about 40% of its electricity consumption during peak months from solar power. It also focuses on adhering to global recycling standards, using recycled materials, following responsible down standards, and obtaining multiple social responsibility certifications.
In parallel with enterprise efforts, VITAS has proposed that the government introduce preferential credit policies for investments in green technology and smart factories and simplify procedures for establishing textile-dyeing industrial zones, a key element in building a domestic supply chain.
In the long term, Mr. Cẩm believes the textile industry needs a comprehensive and sustainable strategy—from regional material planning and high-quality workforce training to trade promotion support and building a Vietnamese brand identity.